Carbonization of Briquettes
Carbonization Processes
Direct use of agricultural residuals as fuel is normally characterized by low efficiency. Also the low bulk density of the residues often makes them uneconomical to store or transport. One method to overcome there difficulties is to densify and carbonize them. The carbonized briquette develops a higher temperature in stoves and furnaces and has the advantages of relatively smokeless combustion. As it dose not rot and it not attacked by termites, fungus, etc., the storage losses are relatively very low.
Unless burnt in controlled conditions, biomass-based fuels tend to produce appreciable quantities of smoke, problematic if the fuel is to be used in indoor environments. A common way to overcome this in briquetting is to carbonise either feedstock or the finished briquette. Carbonisation (or partial pyrolysis) drives off volatile compounds to leave more or less pure carbon; the biomass is heated to within a critical temperature band (around 300℃) but with a restricted supply of air so that it does not ignite. Various processes options are available including simple earth kilns to more complex retorts that make use of the volatile compounds in heating the process.
As mentioned, the raw material used is sawdust from various species of tropical wood. The moisture content of these green or fresh sawdust varies from about 40-50%. The green sawdust are first screened to remove contaminants and oversized particles. They are then dried to a moisture content of about 8-10% in an impulse dryer with hot air that is generated using wood wastes. The fairly dry sawdust are then fed into a screw type briquetter for compaction into briquettes. The density of the briquettes formed is around 1200kg/m. The briquettes that leave the briquetting machine are hot and slightly roasted on the outside. As such they have to be left in the open to cool. The cooling process further enhances the binding between the sawdust particles.
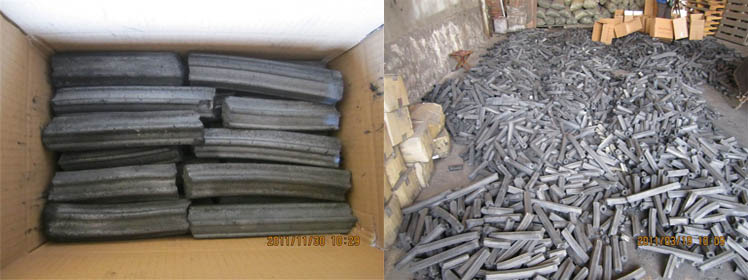
The sawdust briquettes are then neatly arranged on a bugee which is an open cart with only 2 end walls, with air flow homes at the lower portion and rollers at its undersurface. The loaded bugees are then pushed into the carbonization kilns. After the bugee is pushed into place inside the kiln is then sealed. The carbonization process is started by putting a few pieces of lighted briquettes on top of the pile before the bugee is pushed into the kiln. The sawdust briquettes are carbonized at a temperature of 850-875 degree for 108 hours with air flow that is controlled at various stages of the process. A good control of the air-flow is essential in ensuring that good quality charcoals are produced.
When the carbonization process is complete which is indicated by the emission from the chimneys becoming invisible, the bugess with the red hot charcoal inside are removed from the kilns and immediately covered with sealed boxes which are then completely sealed with sand to avoid any entry of air.
KMEC is one of the earliest and largest biomass briquette press manufacturer that provide our customers with qualified products, competitive biomass briquette price and superior service. With strong technical knowledge and more than ten years of production experience, as well as our competitive price and perfect after-sale service, we have gained good reputation among customers in this field. If you need biomass briquetting press, please feel free to contact us.